Inditex estrena un nuevo material para fabricar prendas de nailon hecho a partir de residuos textiles
Bautizado 'loopamid' y desarrollado junto a la química BASF, supone «un avance significativo en sus esfuerzos para impulsar la reciclabilidad en la industria»
El grupo textil también empleará gas extraído de aguas residuales en La Coruña
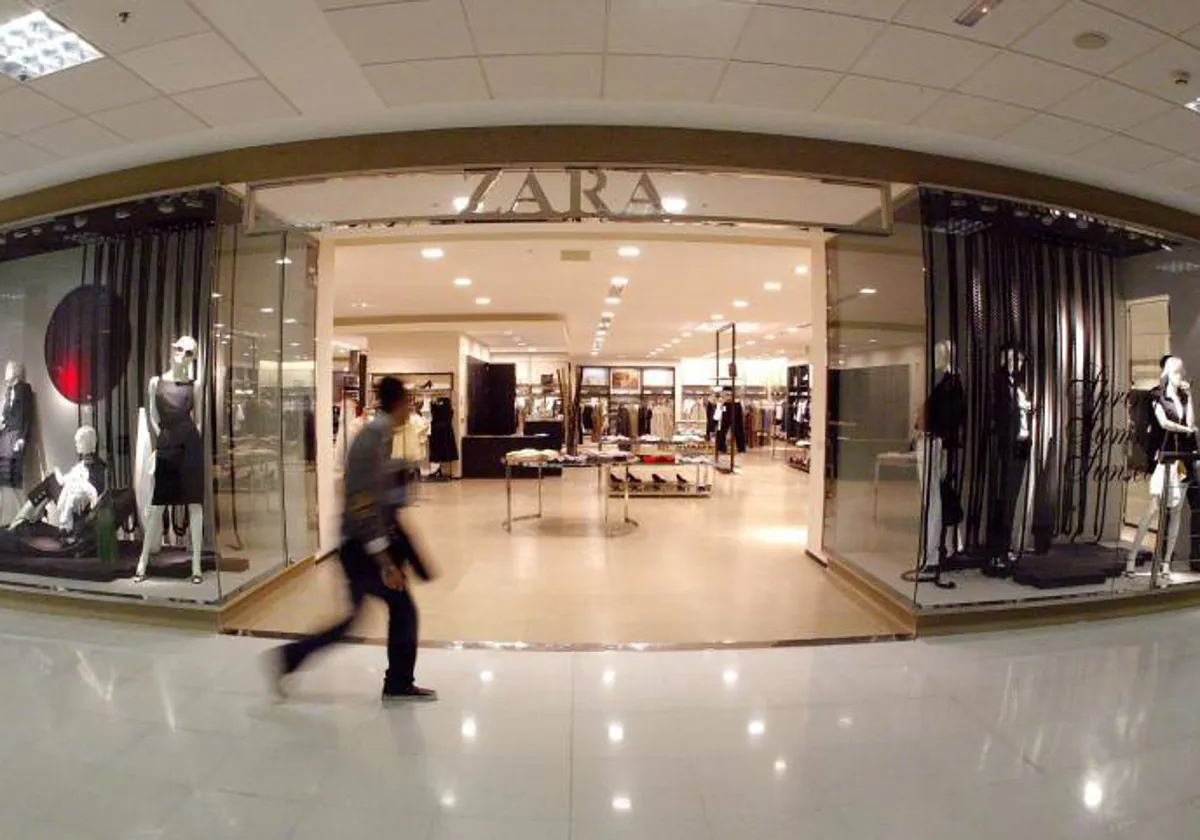
La empresa química BASF y el grupo Inditex acaban de anunciar el lanzamiento de un nuevo producto, bautizado 'loopamid', que supone «un avance significativo en sus esfuerzos para impulsar la reciclabilidad en la industria textil». Se trata de una poliamida 6 reciclada —PA6, también conocida como nailon 6— que supone «la primera solución« basada en economía circular para fabricar prendas de nailon hecha íntegramente a partir de residuos textiles. Zara ha convertido este material en una chaqueta, que ya se encuentra disponible para su compra de forma online, siguiendo un enfoque de «diseño para el reciclaje»: todas las partes del producto, incluyendo el tejido, los botones, el relleno, los velcros y las cremalleras, están fabricadas con loopamid procedente del reciclaje de prendas, afirma la propia marca.
En un comunicado, BASF destaca la importancia de esta «solución innovadora» de cara a mejorar la circularidad en la industria de la moda y reciclar residuos textiles de poliamida 6. Debido a su capacidad para admitir todas las mezclas de tejidos, la tecnología que integra loopamid «permite el reciclaje textil a textil de residuos postindustriales y postconsumo« y posibilita que las fibras y los materiales se puedan reciclar múltiples veces. Al mismo tiempo, abunda la firma, las características del material resultante son idénticas a las de la poliamida virgen.
«BASF ha alcanzado un hito importante hacia la circularidad en la industria de la moda, siendo pioneros en nuestro enfoque para cerrar el círculo de los textiles de nailon», señala el doctor Ramkumar Dhruva, presidente de la división de Monómeros de BASF. «Nuestra loopamid tiene el potencial de revolucionar positivamente el mercado de PA6. Estamos en el proceso de ampliar nuestra tecnología para servir a nuestros clientes cantidades comerciales. Esta chaqueta producida por Inditex es la prueba de que la circularidad es posible y estamos ansiosos por impulsar aún más la transformación sostenible de la industria textil«, declara.
Inditex ha colaborado con otros grupos de la industria para integrar la loopamid en los distintos componentes de las prendas, incluidos tejidos, cremalleras, botones, rellenos, velcros e hilos de coser. Entre otras, ModaRe, un programa de recogida de prendas operado por Caritas, separó y clasificó los textiles desechados para convertirlos en una nueva materia prima; la empresa italiana RadiciGroup ha trabajado en el proceso de transformación del polímero loopamid en varios tipos de hilos con diferentes características; y la multinacional japonesa de productos de sujeción YKK y las empresas multinacionales Velcro también han desempeñado un papel crucial en la utilización de loopamid para crear componentes plásticos para cremalleras, botones a presión, y cierres por contacto.
Javier Losada, director de Sostenibilidad de Inditex, añade que «impulsar la innovación» es la «clave» para lograr un avance hacia «una industria más responsable». «Esta colaboración es un gran ejemplo de cómo, trabajando juntos, podemos utilizar las nuevas tecnologías para transformar los residuos textiles en un nuevo recurso«, sostiene, y «también un primer paso para avanzar hacia una solución circular. No obstante, la industria necesita impulsar nuevas capacidades de recogida y reciclaje para cerrar el círculo y escalar el reciclaje de residuos posconsumo», recuerda.
En la colaboración entre BASF e Inditex, la primera pretende duplicar sus ventas vinculadas a soluciones para la economía circular, hasta los 17.000 millones de euros de cara a 2030; mientras que la segunda trabaja para que, en ese año, el 100% de sus productos textiles estén fabricados exclusivamente con materiales con una menor huella ambiental. Como parte de este compromiso, afirman desde el grupo, esperan que el 25% de las fibras textiles se fabriquen con materiales de última generación que hoy no existen a escala industrial, un 40% de materiales reciclados y un 25% de fibras procedentes de la agricultura orgánica y regenerativa.
Esta funcionalidad es sólo para suscriptores
Suscribete
Esta funcionalidad es sólo para suscriptores
Suscribete